5 Reasons Why Machine Shop Ownership Is Changing in 2022
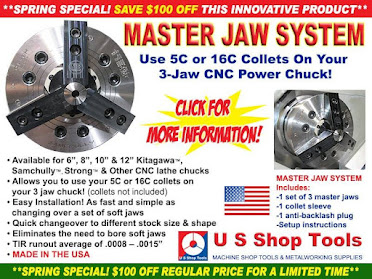
Machining businesses have been changing ownership or leadership with greater frequency in the last couple of years than at any other time during the quarter-century I’ve been watching metalworking. We are in a season of fundamental change for machine shops — change at the tops of these enterprises — and that change continues today. The most recent example I encountered was a soft transition, a shop owner I regard highly described to me his determination to step back and let his daughters now run things. Other cases have involved more formal acquisitions and mergers. I can’t prove the claim I am making here; machine shops are often small, independent businesses, and I do not know of a data set that quantifies their rate of ownership change. But anecdotally, the conclusion has been hard to miss. I see shops today more frequently brandishing new names or taglines indicating recent ownership change or working through ongoing ownership transitions. We wanted to understand and bear witnes